Man skal alltid prøve å følge drømmene, og slik har det
alltid vært. Et eksempel på hvorfor finner vi i Frankrike, hvor bilgeniet
Ettore Bugatti drømte om å lage egne biler da han jobbet for Gasmotoren-Fabrik
Deutz tilbake i 1908.
løsninger som ingen tidligere hadde tenkt på. Resultatet ble enestående. Da den franske luftfartspioneren Louis Blériot fikk
prøvekjøre bilen, ble han så imponert at han ba Bugatti serieprodusere den med
en gang. Året etter realiserte unge Bugatti drømmen, og siden kom han
opp med nye løsninger som for eksempel en hul frontaksel og lettvekst
aluminiumsfelger. 100 år senere produserer Bugatti noen av de mest imponerende
hyperbilene verden har sett, deriblant de nye Chiron Pur Sport and Chiron Super
Sport 300+. Og Bugatti fortsetter å drive bilindustrien framover med nye
løsninger. ‒ Bugatti handler om en luksuriøs stil og eksepsjonelle
biler i fransk stil, men det er et merke som også står for nyskapende
teknologi, sier Stephan Winkelmann, president for Bugatti. ‒ I tillegg til den ikoniske 8.0-liters 16-sylindret motoren
med 1.500 hestekrefter, er teknisk innovasjon like mye del av merkevaren vår ‒ for
eksempel er komponentene våre laget av titan eller en spesiell legering som er
produsert av 3D-utskrift.
teknikken en stund allerede. Men det er svært komplisert å produsere slike
deler ut av 3D-printing, men det stopper ikke det franske supermerket. Som de eneste i bilindustrien bruker Bugatti 3D-utskrift for å produsere deksler rundt eksosrørene laget av titan. Dekselet er den første synlige delen som er 3D-printet i metall som er offisielt godkjent for bruk på veiene. Her den særs imponerende «La Voiture Noire», verdens dyreste nybil.
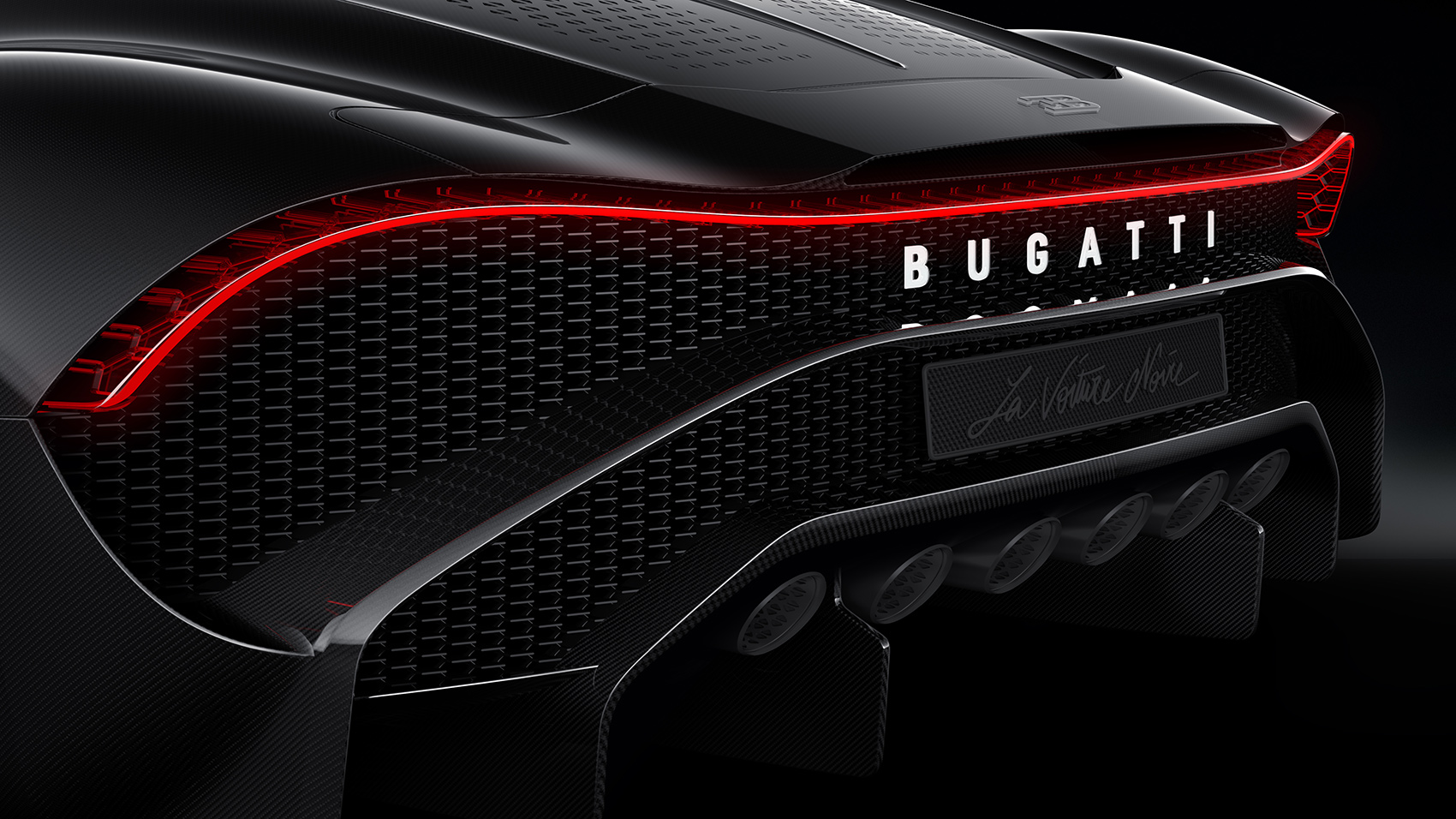
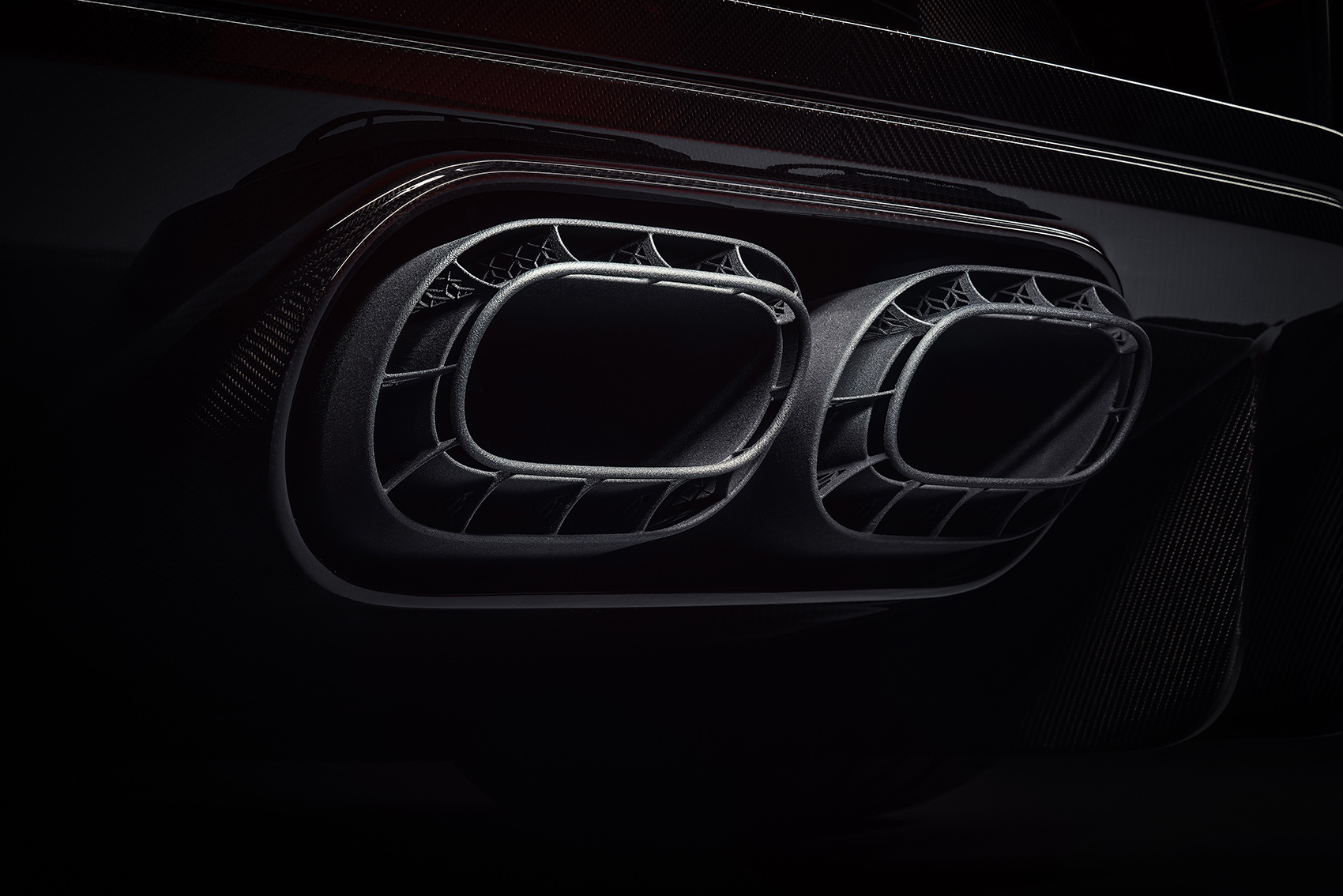
deler hjemme. De bruker fire 400-watts lasere som på samme tid skriver ut
titan som brukes til komponenten, og veggen er på det tynneste kun 0,4 mm. Rundt
4.200 lag med metallpulver settes opp på hverandre og blir deretter smeltet
sammen. For som på Ettores tid handler det meste om vekt. ‒ Der det var mulig designet vi dekselet til Chiron Pur
Sport med ett lag for å redusere vekten ytterligere, sier Nils Weimann, leder
for karosseriutvikling hos Bugatti. Det franske merket har benyttet 3D-teknikken siden 2018, og modeller som Chiron Sport, Divo, «La Voiture Noire» og Centodieci har alle 3D-printede komponenter. På Chiron Sport dekker dekslet fire eksosstusser, og det er
langt fra kun visuelle fordeler. De hjelper til å lede bort varmen, og det
trengs. For med 1.500 hk og en toppfart på opptil 420 km/t, teller alle
detaljer. Og med 2,2 kilo veier den 3D-printede delen 800 gram mindre
enn et normalt deksel. Og det er i ånden til Ettore Bugatti, som bygde biler
med mottoet: «Vekt er fienden». Mange andre i bilindustrien har også tatt i bruk 3D-printing,
men på et litt annet nivå. Cupra, dette litt mer sportslige merke til Seat, benyttet
seg for eksempel av 3D-printing da de utviklet racerbilen Leon Competición.
Denne fikk 3D-printede deler som de utvendige speilhusene, luftinntak og
kjøleinntak. I tillegg til at det er en rask produksjonsmåte førte også 3D-printing
til økt stabilitet, høyere hastigheter og enda bedre sikkerhet ‒ tre ting alle
liker. Her plasserer de grillen på plass:
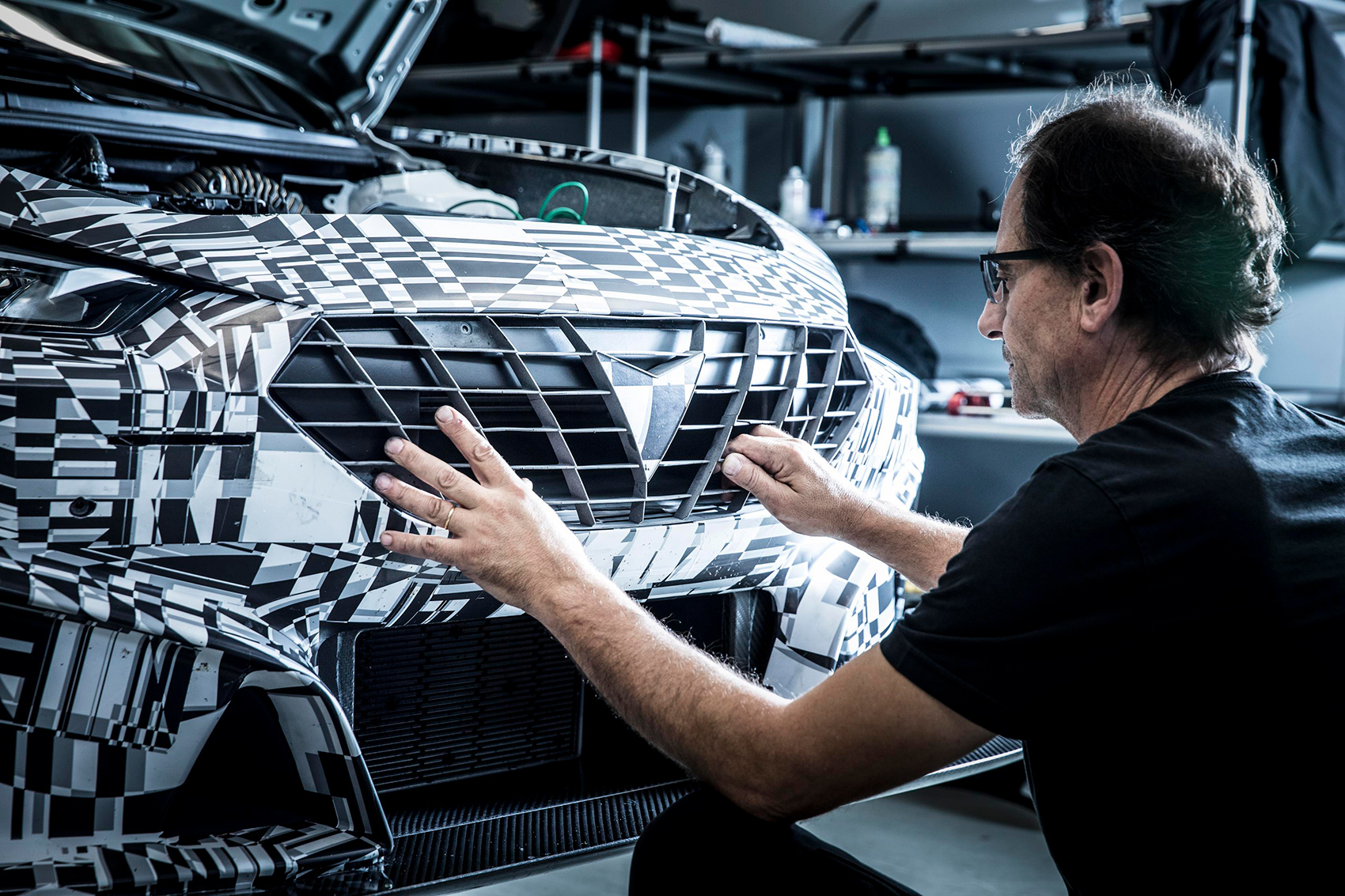
rundt 3,3 sekunder, og med en 2-liters motor med 340 hk har den en toppfart på
290 km/t. Litt takket være 3D-printing. Les også: